Porosity in Welding: Identifying Common Issues and Implementing Ideal Practices for Prevention
Porosity in welding is a prevalent issue that frequently goes unnoticed until it causes substantial issues with the integrity of welds. This usual defect can compromise the stamina and longevity of bonded frameworks, posing safety dangers and leading to expensive rework. By recognizing the source of porosity and carrying out reliable prevention methods, welders can substantially enhance the high quality and reliability of their welds. In this conversation, we will check out the vital factors adding to porosity formation, examine its destructive impacts on weld performance, and talk about the most effective techniques that can be embraced to decrease porosity incident in welding procedures.
Typical Causes of Porosity
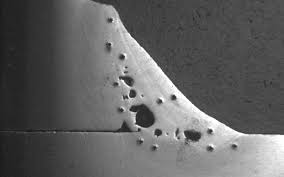
Utilizing filthy or wet filler products can introduce impurities right into the weld, adding to porosity concerns. To mitigate these common causes of porosity, comprehensive cleansing of base metals, correct shielding gas option, and adherence to ideal welding parameters are essential techniques in achieving high-grade, porosity-free welds.
Effect of Porosity on Weld Top Quality

The existence of porosity in welding can substantially compromise the structural honesty and mechanical residential properties of welded joints. Porosity develops voids within the weld steel, compromising its general stamina and load-bearing capacity.
Welds with high porosity levels often tend to exhibit lower impact stamina and lowered capacity to flaw plastically before fracturing. Porosity can hamper the weld's ability to effectively transmit forces, leading to early weld failing and possible security dangers in important structures.
Finest Practices for Porosity Prevention
To boost the structural honesty and high quality of bonded joints, what certain procedures can be executed to minimize the occurrence of porosity during the welding process? Using the proper welding technique for the specific product being welded, such as adjusting the welding angle and weapon placement, can better protect against porosity. Normal assessment of welds and prompt remediation of any issues recognized during the welding procedure are crucial practices to prevent porosity and produce top quality welds.
Importance of Appropriate Welding Strategies
Carrying out correct welding methods is vital in making sure the architectural honesty and top quality of bonded joints, building on the structure of effective porosity avoidance actions. Welding techniques straight impact the total strength and sturdiness of the welded structure. One essential element of proper welding strategies is maintaining the appropriate warmth input. Extreme warm can result in enhanced porosity as a result of the entrapment of gases in content the weld pool. Alternatively, insufficient warmth might lead to insufficient blend, producing possible powerlessness in the joint. Furthermore, utilizing the ideal welding specifications, such as voltage, existing, and take a trip rate, is critical for achieving audio welds with minimal porosity.
Moreover, the choice of welding process, whether it be MIG, TIG, or stick welding, must line up with the certain requirements of the job to ensure optimum outcomes. read Appropriate cleansing and prep work of the base metal, along with picking right here the right filler product, are likewise necessary components of skillful welding methods. By sticking to these finest practices, welders can lessen the risk of porosity formation and produce top notch, structurally audio welds.
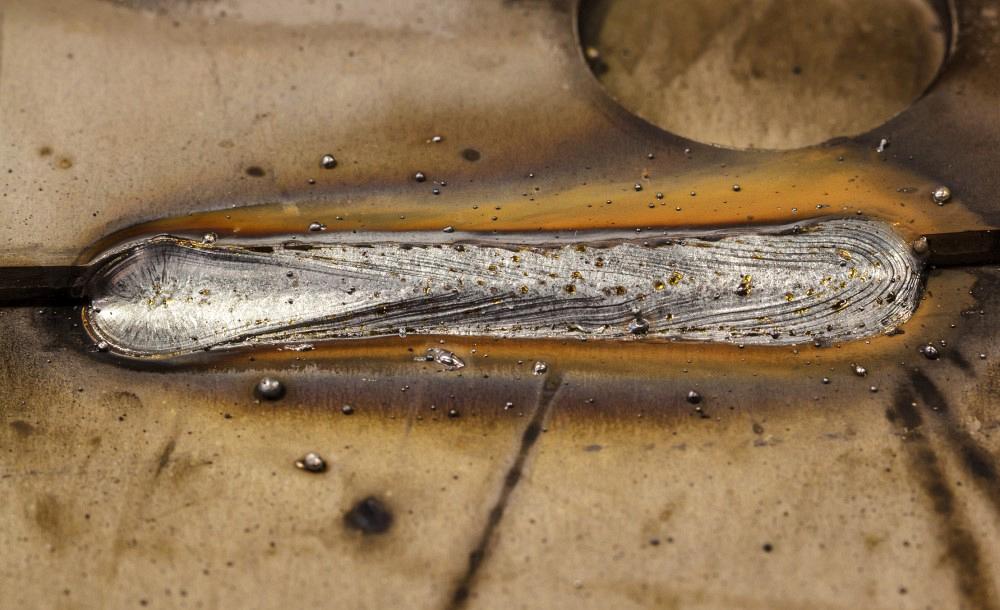
Checking and Quality Control Steps
Quality control procedures play a critical function in confirming the stability and reliability of bonded joints. Checking procedures are important to identify and avoid porosity in welding, ensuring the stamina and longevity of the last product. Non-destructive testing techniques such as ultrasonic screening, radiographic testing, and aesthetic examination are commonly used to identify possible issues like porosity. These methods enable for the analysis of weld top quality without endangering the honesty of the joint. What is Porosity.
Post-weld evaluations, on the various other hand, analyze the final weld for any type of problems, consisting of porosity, and validate that it fulfills defined criteria. Executing a thorough quality control plan that consists of comprehensive testing procedures and assessments is vital to lowering porosity problems and making certain the total quality of bonded joints.
Final Thought
In verdict, porosity in welding can be a typical issue that affects the quality of welds. By recognizing the usual sources of porosity and executing best practices for avoidance, such as proper welding strategies and screening measures, welders can guarantee excellent quality and dependable welds. It is important to prioritize prevention methods to minimize the occurrence of porosity and keep the honesty of welded frameworks.